MEM234027A- Plan and Manage Materials Supply for an Engineering Project or Manufacturing Operation Assignment Help
GET EXCEPTIONAL EXPERTS TO PERFORM YOUR COLLEGE OR UNIVERSITY ASSIGNMENTS IN NO TIME. EXPERTSMIND.COM IS THE ONLY ONLINE ASSIGNMENT HELP SERVICE YOU WILL EVER ASK FOR!
Case Study 1
1.Centralized manufacturing structure (CMS) comprises of a single factory or location which has the capacity to reduce per unit production cost by including adaptive and versatile equipment. The set-up also streamlines the procedure such that it can produce various product types in numerous quantities according to the rate of demand and sale. CMS organizations are considered as more effective and efficient for making excellent quality management and successful business decisions. Working standard at CMS provides the opportunity for better product forecasting, creates local jobs, efficient use of limited supplied resources, and consistent production routine. In addition to this, the structure also helps in lowering the cost of raw material and operation, because of their strategic decision for placing location nearer to the source of supply. Based on the case analysis prepared by the Graduate student, it can be learned that CMS has the potential to reduce manufacturing cost around 3% as compared to decentralized manufacturing structure. In contrast, the corresponding production schedule efficiency and inventory turn rate was found to be higher. Likewise, the centralized manufacturing structure has more stable contact pricing, improved material management system, minimum per unit cost, which is resultant from their efficient strategic framework for manufacturing. It is apparent that centralised manufacturing structure is more suitable and convenient for a smaller firm structure as it has limited capital and resources (Lara and Grossmann 2016). In addition to this, the decision makers and owners of these smaller firms are located at the front line of business operation, which help them to handle the whole production line. Despite of these benefits CMS also has some negative aspects, such as costly and time consuming for making customized products, as revealed from the case analysis.
In the present case study, it is evident that Electrolux Company has used decentralised manufacturing process instead of centralized manufacturing process (Pekgün, Griffin, and Keskinocak 2017). In its decentralized manufacturing structure, the overall management operational activities are executed by the business sector boards located all over the world. For the major appliances the company has geographically defined business sectors, while for small appliances and professional products it has global business sectors. Moreover, due to its global presence, the responsibilities include product development, manufacturing and purchasing, are categorised and distributed among various department. In total, it has 52,000 global employees and it is not possible in CMS to handle such a huge employee on global scale.
The given case study has very limited description related to Electrolux’s manufacturing structures. If I would be given the responsibility to prepare the report on the given case study, then inclusion of the global as well as local business sectors involved in managing the operational activities, would also be discussed in the given context. Apart from this, in my opinion, it is also important to mention involved decision making bodies of the company. For instance, Electrolux consists of Global major appliances leadership team (MALT) which comprises of CFO, president, Chief marketing officer, Chief technology officer, Chief design officer, and head of product board.
2.In according to the analysis of data present in Electrolux website, it is expected that during the period from 2018 to 2022 global hubs, market will increase at a compound annual growth rate (CAGR) of 8.3%. The reason behind the expected growth in the coming years is the shift of customer’s preference towards modular kitchen rather than the old traditional kitchen. Thus, the company plans to focus more towards the designing of modular kitchen in most of the residential projects; providing maximum kitchen space as well as suits the customer's preference. Additionally, Electrolux also focusses to fulfil the increased demand of built in induction hobs in the modular or remodelling kitchens. Report suggests that, there will be an increase in the market growth based on new designs and product innovation. In this direction, the company plans to introduce offers such as temperature control, child lock, sensory panels and timer for attracting new as well as existing customers (Ioan, Battistella, and De Toni 2016).
3.In the present case scenario, the graduate student has adopted methodology of face to face questionnaire survey in the Electrolux Group. The given student anticipated various examples of waste reduction and for this purpose he visited Electrolux plant on June 16th, 2011. In this context he contacted staff engineer who directed him towards a study in the dishwasher assembly line reducing waste. For the collection of data, the method comprises of interacting with all the participants who took part in 'waste reduction’ study. Further, the employees explained him the importance of 5S for eliminating waste, which were included in the case analysis. Overall, the analysis present is informative and include detailed comparison (before and after) for the implementation scope (Regmi, Waithaka, Paudyal, Simkhada, and Van Teijlingen 2016).
In my opinion, the graduate student can also use another alternative method for data collection such as online survey, for getting more explicit form of information. In the online survey the student can put the key questions for the participants where they can respond individually and clearly to each questions. For this purpose, it is important to prepare a set of relevant and important questions related to waste reduction and mitigation. In conjunction to this, it is also important to invite the employees of the Electrolux plant as the participants of online questionnaire. Finally, the responses can be gathered, analysed and used in the report, in similar to the one presented in given case analysis. The data collected from online survey will be more exact and precise results for report writing.
4.
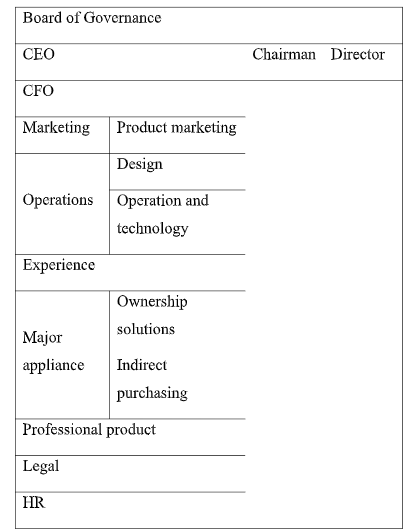
The above chart shows the organizational structure and the reporting lines of corresponding department or authority is shown besides (The official board, 2019). The top most authoritarian is the board of governors that mainly have responsibilities of reviewing the policies, authorizing the reports, and implementing the requisite changes. Reporting line for board of governors include, chief executive officer, chairman, and directors. The chairman and director have their requested responsibilities with reference to the existing units, and existing activities, and reviewing the workflow. However, to all the individual operating units, the reporting concern is the board of governance which is situated at the headquarters.
Chief financial officer is the unique authority concerning with the cash flow, liquidity, capital assets, and infrastructure. They have the responsibility to prepare the financial statement and audit report for CEO. Are there reporting units include marketing, operations, experience, major appliance, professional product, illegal activities, and HR which have the responsibility to report to the CEO. Subordinates reporting line in this organizational structure include mainly for operations and major appliance unit. The responsibilities of operations include inclusion of technology and innovations as well as design requirement according to the market needs. Likewise, experience section mainly focuses to competencies and responsibilities of employees which in turn also have working collaboration with HR department. The legal department will take care of the policies, guidelines and regulatory measures with reference to local and national authority. Other activities within the organization such as recruitment, selection, training, and employment benefits were controlled and regulated by HR department.
5.The 5S is defined as the lean method for optimizing workplace and minimizing waste. It comprises of five consecutive steps which can help any organization to maximize its efficiency:
•Sort - In this process the required tools, materials and instructions will be separated from those which are unnecessary within the work area.
•Straighten - Here all the tools files equipment resources in data are sorted and organized for easy and quick location and use. For this purpose, all the tools, equipment and storage locations should be well labelled (Omogbai, and Salonitis, 2017).
•Shine - All the trash, dirt, and grease will be cleaned and removed to create a safe work area for the employees.
•Standardize - Workforce are motivated and advised to follow the above three steps regularly for maintaining a perfect workplace.
•Sustain - 5S is created as a cultural part and corporate philosophy of the organisational performance management system.
6.Based on case study, Electrolux has implemented 5S approach in its work process. It is evident that Electrolux has only used the first three steps (Sort, straighten, and shine) for organisational development. The case study shows that application of 5S sequence, there is 51 % drop in inventory level of Electrolux which is from 31400 to 15400. In addition to the 51% inventory level reduction, there was also a 30% reduction in cost which eventually increased 5% productivity rate. The primary technique used in 5S metrology is lean manufacturing tool, where after the production of product is over there is need to eliminate waste (Randhawa and Ahuja 2017). However, other than the 5S methodology, there are certain other methodologies which have the potential to give better cost reduction strategy along with quality production and risk minimisation. One such methodology is Six Sigma where data analysis is done rigorously through statistical analysis (such as hypothesis tests, ANOVA, and control chart) as well as analytical tools (such as heuristics). This is my six has two different flavors: 1) DMAIC (Define Measure Analyze Improve Control), 2) DMADV (Define Measure Analyze Design Validate). DMAIC focus on Six Sigma multi focus for business problems and converting these issues into performance measure and identifying the root cause associated with these issues. In particular, this is basically a mythology which emphasize on improving and well set process into a more productive one. Similarly, DMADV Six Sigma focuses on designing new products and services to meet the requirement of customers. DMADV is more suitable for a large organization like Electrolux (NPI) New product introduction and (NPD) New product development schemes (Akpolat, 2017). The Six Sigma methodology is highly effective for organisations, during their product development life cycle. Further this it is again characterized into i) black belt six sigma and ii) green belt Six Sigma. This characterization is done on the basis of knowledge, competency level and organizational level at which employees do projects and tasks. The green belt Six Sigma employees of those who lead project within smaller scope, what is the black belt Six Sigma employees leads projects on a larger scale which basically includes the consideration of the whole organization. Among all of them the master black belt employees are considered as the highest six sigma belt who booty is not only knowledge and capability in black belt tool but also have experience in running projects at risk management.
7.Electrolux is highly dedicated and responsible electronic producer in the global market. Its work culture is not only limited to provide a healthy and safe work environment for its employees, but also a better environment for the people around it. Its workplace policy was launched the year 2002 under the name of ‘Workplace Code of Conduct’. The policy compliance ensures that the responsibility of management team and employees of the company to follow the code of conduct. The company’s workplace policy covers child labour, forced labour, health and safety, harassment and abuse, and non-discrimination. Likewise, the policy measures also focuses on working hours, environmental compliance, corruption, and compensation. For example, Electrolux doesn't allow its employees to work more than 48 hours per week. Similarly, it is strictly against employing child labour (younger than 15 years) and encourages to complete their minimum educational requirement. These policies are applicable to all global Electrolux stores. In the same way, Electrolux also facilitates safety policies for its suppliers as well. For effective implementation of these policies and standards, the company conducts risk assessment, training sessions and audit programs for its employees, HR team, and environmental managers of each workplace. The production units within the company are certified under “ISO 14001” standard and ensures safety (Almgren and Demner 2015). The management team is responsible to conduct frequent review and monitoring of the abidance of employees with the policy. In this regard, the suppliers are also requested to co-operate with Electrolux Group while conducting audits and confidential interviews.
8.The purchasing and production policies and procedures of Electrolux acts as a guideline for the professional purchasing staffs in their daily activities. These policies help to establish a healthy relationship not only to internal employees but also with the suppliers. In addition to this, it also ensures the product, services and production activities as an integral part of sustainable environment.
The purchasing and production policies embedded in Electrolux help in i) defining the role of purchasing and production personnel ii) solving operational issues, iii) strengthening buyer and seller relationship, and iv) explicitly describing the social business objectives. It is important to mention that the company have framed various purchasing and production policies based on the review, analysis, and recommendation from experienced group leaders, which includes ethics, reciprocity, and environmental policy. For example, the environmental policy emphasises on implementing ISO 14000 certificate as well as international organisational guidelines for standardisation for business transaction globally. In this context, these policies come under international bill of Human rights, organisation for economic co-operation and development guidelines for multinational enterprises, and conventions of the international labor organization. Apart from this, it also provides an outline for the supplier’s responsibility for shipment of defective material. According to Candan et al (Candan, and Kapucu 2018), the shipment of a single defective product in the just-in-time production environment has the power to close the entire production system. These policy measures are framed for maintaining adequate standards of working as well as for safe practices.
9.The contingency policy of Electrolux aims at reducing the impact of damaging event on the organisational performance along with protecting its integrity, availability, and confidentiality of vital information (Ivanov and Rozhkov, 2017). The senior leaders (chief operating officer) of the group holds the responsibility to plan contingency policy which includes funding, pilot testing and executing. For developing contingency plan, the company identifies the major functional areas required for its business operation. Accordingly, for each functional area contingency plan is developed which is finally assimilated as a whole for the entire organisation. Electrolux contingency plan includes measures like business impact assessment, data backup process, contingent cooperation process, emergency operation process, and disaster recovery plan (Ivanov and Rozhkov, 2017). It is the responsibility of the company’s contingency plan coordinator to communicate the plan with the employees and train them according to their responsibilities. In addition to this, the scope of responsibility also include risk identification and mitigation strategies that can help the company to achieve the objectives. It is also important to note that the management group have also implemented a communication and educational plan to make its employees well informed of sudden changes and aware of individual responsibility. This implementation not only prepares the employees to have knowledge about emergency practices but also strength their competency requirements. Presently, all the necessary information of Electrolux has been stored in online mode, which can be accessed anywhere and anytime. Thus, the IT department ensures that the essential information of the company (such as supply history, sale history) can be maintained or retrieved during any emergency incident.
10.The performance management system of Electrolux includes: i) evaluating performance and assessment, ii) personal performance development planning, and iii) performance review and assessment. Electrolux several performance measures for assessment, such as customer care, output, attaining organisational goals, quality, business and financial awareness, flexibility, and learning targets. For the purpose of personal development planning, it implements project work, training, mentoring and self-managed learning. Performance review and assessment it's collected on the basis of an individual’s achievement, technical competencies, and behavioural impact. The line managers of Electrolux are given the prime responsibility to execute performance management effectively. For evaluation of the performance management these line managers use several methods viz., 360-degree appraisal, self-assessment, feedback program, and reward program. The 360-degree appraisal method is often used by supervisors and managers of Electrolux, as it helps in providing available data regarding and employee’s performance and behaviour. In self-assessment method the employee will analyse their own performance violin competency-based assessment the supervisor will examine the employee’s capabilities and skills (Van Dooren, Bouckaert, and Halligan 2015). The continuous improvement policy of Electrolux aims at improving the business processes and practices in order to drive organizational success and stakeholder satisfaction.
Different types of software used by Electrolux for performance management are: AssessTeam, Zoho people and Performance Pro.
The resource planning method used by Electrolux is ERP (Enterprise Resource Planning). ERP has been implemented by Electrolux Group since 2002. Presently the company has installed cloud ERP system which facilitates, security, low cost, and improved work process.
ACQUIRE ONLINE ASSIGNMENT HELP SERVICE AND FULFIL ALL YOUR ACADEMIC REQUIREMENTS UNDER ONE ROOF!
Case Study 2
1.The National Environmental Agency (NEA), Singapore is an organisation performing under the Ministry of Environment and Water Resources. It aims at creating a green and clean environment in Singapore by partnering with public, private and people sector. This government authorises and implement plans to protect the air, water and land of Singapore, for ensuring a sustainable development and quality life for future generation. In the present scenario, Mr Charles Lee is the acting Assistant Director of NEA (Tan, Lee, and Tan 2016). The said organisation is also involved in collaboration with Asian Environmental Compliance and Enforcement Network (AECEN) in 2005. The current policies for waste management in Singapore includes Environmental Public Health Regulations including the management of general waste, Public health Act, and Environmental Public Health Regulations including the management of toxic industrial waste.
2.The national environment agency and Singapore hotel association launched the 3Rs programme which comprises of reduce reuse and recycle. The initiative aims to achieve a better waste management technique and maximizing waste recycling rate. According to the given case study, the 3Rs initiative managed to put off “3000 tons per day waste to” energy from once every 5 to 7 years to every 10 to 15 years. The program also partners with different hotels for waste audit, waste reduction and waste recycling (Hashim, Mohamed and Redza 2017).
Despite of being a dense and populated country, Singapore effectively manages its waste through its initiative program “Singapore packaging agreement”. The agreement offers a flexible approach towards manufacturers retailers and importers for bringing cost-effective solution by reducing packaging waste. To encourage participation of more companies the program provides awards to active participants. Overall, the programs not only provides clean environment to the present generation but also safeguards the requirement of future generation.
GET THE FEATURED ASSISTANCE AND QUALIFIED TUTORS AT MEM234027A- PLAN AND MANAGE MATERIALS SUPPLY FOR AN ENGINEERING PROJECT OR MANUFACTURING OPERATION ASSIGNMENT HELP!
Access our ECA Graduate Institute Assignment Help and tutor Services for related courses and units such as:-
- MEM23063A- Select and test mechanical engineering materials assignment help
- MEM23064A- Select and test mechatronic engineering materials assignment help
- MEM23111A- Select electrical equipment and components for engineering applications assignment help
- MEM23112A- Investigate electrical and electronic controllers in engineering applications assignment help
- MEM23113A- Evaluate hydrodynamic systems and system components assignment help
- MEM23114A- Evaluate thermodynamic systems and components assignment help
- MEM23041A- Apply basic scientific principles and techniques in mechanical engineering situations assignment help
- MEM23051A- Apply basic electro and control scientific principles and techniques in mechanical and manufacturing engineering situations assignment help
- MEM23061A- Select and test mechanical engineering materials assignment help
- MEM23062A- Select and test mechatronic engineering materials assignment help
- MEM23071A- Select and apply mechanical engineering methods, processes and construction techniques assignment help
- MEM23072A- Select and apply mechatronic engineering methods, processes and construction techniques assignment help