ARE YOU LOOKING FOR RELIABLE ENGIN2503 MINING ENGINEERING ASSIGNMENT HELP SERVICES? EXPERTSMINDS.COM IS RIGHT CHOICE AS YOUR STUDY PARTNER!
ENGIN2503 Surface Mining Operations and Equipment - Federation University
EXPERTSMINDS.COM ACCEPTS INSTANT AND SHORT DEADLINES ORDER FOR ENGIN2503 MINING ENGINEERING ASSIGNMENT - ORDER TODAY FOR EXCELLENCE!
1. Explain the terms
a. Bench and overall slope angles
Bench angle is the angle between the ledge (above which minerals are mined from the bench face) with the ground of the mine i.e. the horizontal angle the line connecting bench toe to bench crest. Overall slope angle is the angle made by line connecting toe of bottom-most bench to crest of top-most crest. It depends on the rock type (strength), the geologic structure and water conditions.
b. Overall, break even and immediate stripping ratios, with reference to the open pit mining method
With reference to open pit mining, stripping ratio is amount of waste that should be removed from a given quantity of ore. Formula for it is:
Stripping ratio (SR) = Waster (tons) / Ore (tons)
Overall stripping ratio is the total amount of material removed.
Break-even stripping ratio is the instantaneous stripping ratio at the pointwhere the cost of stripping the waste exactlyequals the value of the ore uncovered.
Intermediate stripping ratio is ratio of amount of waste that is removed from the total quantity of ore during mining.
c. Mineral resource and Ore reserve
Mineral resource is a bulk of material which has economic viability to be used for commercial purposes. It can be inside or on earth's crust.
Ore resource is a sub-part of mineral resource that is of present economic interest.
d. Cut-off grade
Cut-off grade is the minimum grade for a ore (mineral or metal) to be termed as commercially viable for mining. Ores found below this grade are termed as waste.
e. Powder Factor
Powder factor, also called specific charge, is the ratio of mass of explosive required to break a unit quantity of rock in a mine. Depending upon the softness or hardness of rock, the powder factor changes. In simple words, Powder Factor is a relationship between how much rock is broken and how much explosive is used to break it.
f. Charge density
For surface mining during surface-blast design, charge density denotes weight of explosives per unit square of borehole.
DO YOU WANT TO EXCEL IN ENGIN2503 MINING ENGINEERING ASSIGNMENT - ORDER AT EXPERTSMINDS!
2. An open pit mine employs ANFO at a density of 0.8 g/cc as its explosive. Given the following details, determine the blasthole spacing.
- Blastholes are vertical and bench height is 12m.
- Burden and spacing of blastholes are the same, i.e. B = S.
- The specific gravity of the rock is 2.5.
- The powder factor is 0.5 kg of explosive per m3 of rock.
- Hole diameter is 225 mm.
- Stemming column length is 3 m and subdrill is 2m.
If ANFO has a cost of $1050 per tonne, what will be the cost of explosives per tonne of rock?
For vertical blast holes:
Explosive density = 0.8 g/cc = 0.8e-9 tonne/mm3
Bench height (H) = 12 m
Burden spacing (B) = blast hole spacing (S)
Powder factor = 0.5 kg/m3 = 0.5e-12 tonne/mm3
Hole diameter = 225 mm
Stemming column length = 3 m
Subdrill = 2m
Total hole depth = Bench length + Subdrill length = 12+2 = 14 m
Explosive column height (PC) = Total hole length - Stemming column length = 14-3 = 11 m = 11000 mm
Powder factor of a single borehole is given by
PF= (PC X (0.34ρ) X d^2)/(B X S X H/27)
From the above equation
0.5E-12 = (11000 X (0.34X0.8E-9) X ?225?^2)/(B X B X 12000/27)
Blast hole spacing, B=26.1 m
Weight of 1 m3 of rock = specific gravity x 1000 kg = 2500 kg = 2.5 tonne
Amount of explosive required for 1 m3 of rock = 0.5Kg
Amount of explosive required for 2.5 tonne of rock = 0.5 kg.
Explosive required for 1 tonne of rock = 0.5/2.5 = 0.2 kg. = 2e-4 tonne
Cost of explosive = 1050 x 2e-4 = $0.21
SAVE TOP GRADE USING ENGIN2503 MINING ENGINEERING ASSIGNMENT HELP SERVICE OF EXPERTSMINDS.COM
3. Explain various deciding factors related to choice of surface mining over underground mining methods
Surface mining method is performed for mining of minerals, metals or coal. Rigorous planning, scheduling and execution is needed for surface mining plan. There are many steps involved in surface mining which are, 1) removing trees and other fauna over the site of mining, 2) Assessing the soil type and removing the top loose soil, 3) excavation of top hard layer of site land to expose the first layer of ore seam, 4) exposed hard seam is to be open and excavated by the means of explosives, 5) deploying earth moving equipment to take out ore and overburden from mining bench, 6) deploying transport methods (conveyor, trucks etc.) to remove ore and overburden from mining site, 7) processing the extracted ore in plant, 8) filling back the extraction site after completion of mining [1]. Considering all the above steps, there are many factors which are needed to be considered for us to decide on type of mining method.
Underground mining is another type of mining method where in the coal, mineral or metal resources are dug deep from hardest parts of strata. These type of mines are usually completely enclosed and it is worked on from remote locations in many cases. Transport needs for underground mining are high and train-tracks sort of heavy weight carrier are needed as transport mechanisms.
Above explained are the 2 broad methods for mining anore seam which are surface mining and underground mining. Based on the explanation, there are many factors which method is preferred, these factors are classified in 3 broad categories, which are technological factors, economic factors and social factors. Parameters considered for selection of appropriate mining method are following:
A. Technological factors -
a. Number of seams in the coal mine
b. Thickness and steepness of each seam
c. Nature of strata lying over the seam
d. Thickness of strata lying over the seam
e. Quality of coal seams
f. Surface topography
g. Surface features
h. Transportation networks available
B. Economic factors -
a. Energy demand and its growth curve
b. Supply and source of alternate energy sources
c. Cost of alternate energy
d. Coal quality
e. Cost of coal preparation
f. Selling price of coal
g. Cost of production
h. Environment legislation
C. Social factors
a. Prior history of mining in the area
b. Ownership patterns
c. Availability of labour
d. Local or regional government support
Mostly it is technological factors which play a major role in deciding which mining method is best suited.
SAVE YOUR HIGHER GRADE WITH ACQUIRING ENGIN2503 MINING ENGINEERING ASSIGNMENT HELP & QUALITY HOMEWORK WRITING SERVICES OF EXPERTSMINDS.COM
4. Discuss the concept of stripping ratio and how haul road gradient, bench, stack and overall slope angles affect it
Stripping ratio is very important measure in open-pit mining which is a ratio of waste material to total ore in the mine. In other words, it shows the amount of waste material (also called as burden) which should be removed for a given amount of ore to be extracted.
For example, if stripping ratio is 4:1, it signifies that for mining 1 tonne of ore, it requires 4 tonnes of waste rock.
Following are different types of stripping ratios that are used:
i) Volumetric / Geometric stripping ratio
ii) Break-even stripping ratio
iii) Limiting stripping ratio
iv) Instantaneous stripping ratio
v) Average stripping ratio
vi) Overall stripping ratio
vii) Incremental stripping ratio
Haulage is a procedure of removing ore and overburden from open-pit mines for which haul roads are designed. Haul road gradient is necessary for those spiral roads to have a slope. Thehaul road gradient actually affect mine parameters such as overall angle, bench angle and stack slope angle hence affects stripping ratio. Haul roads are used for transportation of ore and overburden out from the mining site. Mostly same haul roads are used for both ways traffic i.e. incoming as well as outgoing. Since while going inside, trucks enter empty and hence it is necessary to design haul road gradient in such a way that safety is assured. For most of the mines, as a rule of thumb, haul road gradient are typically set in the range of 8% to 15% but mostly depends on pit limit on the mine [2].
With overall slope angle increase, the stripping ratio of a mine decreases as shown in figure below. This is because with increase in overall slope, the availability of ore compared to waste generated decreases. Similar relationship of stripping ratio is applicable with both bench as well as stack slope angle.
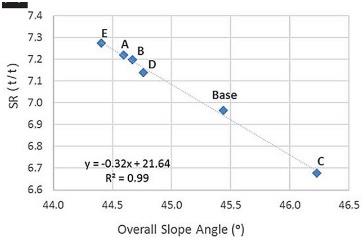
DONT MISS YOUR CHANCE TO EXCEL IN ENGIN2503 MINING ENGINEERING ASSIGNMENT! HIRE TUTOR OF EXPERTSMINDS.COM FOR PERFECTLY WRITTEN ENGIN2503 MINING ENGINEERING ASSIGNMENT SOLUTIONS!
5. Illustrate with a suitable diagram, how waste overburden and ore-body geometry dictates the choice of surface mining method
There are 4 different types of surface mining methods:
I. Contour strip mining
II. Area-strip mining
III. Open-pit mining
IV. Auger mining
Ore-body geometry is the very first factor which governs the selection of surface mining method. If ore seam outcrops is located in rolling or hilly terrains then contour mining is chosen as surface mining method [3]. Area strip mining is selected at the locations where ore-body geometry is flat or terrain is flat. If the terrains are steep or uneven and ore-bodies are thick, then open-pit mining is best suited. Auger or highwall mining is a type of contour strip mining which is used to extract deep ores in any ore-body by drilling holes. All these different types of orebody geometries are illustrated in the figure below.
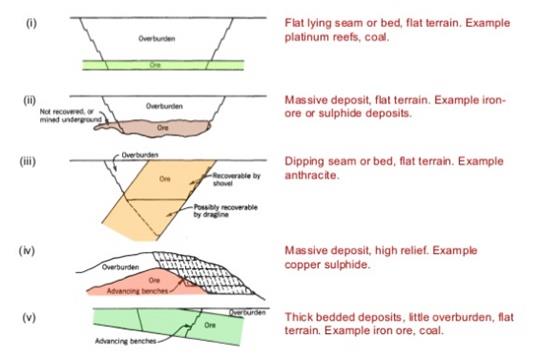
Waste overburden is governed by ore type and ore-body geometry. If the overburden is to be removed above ore-seam in the hilly areas then contour strip mining method is selected. Open-pit mining method is used where thick ore-seam is covered by thick or thin overburden. If the ore is located deep, then auger mining method uses drilling and removes over-burden. This way, depending on the extent of waste overburden, the method of mining is selected.
6. What is meant by "break-even stripping ratio" and what factors would you consider when you need to determine its value?
Break-even stripping ratio is the instantaneous stripping ratio when the cost of stripping the waste or overburden exactly equals the total amount of ore uncovered. In other words, it is the stripping ratio at which costs of mining the ore and waste are same as the revenue for that mine of ore.
Break-even stripping ratio is often calculated for the last increment mined inside the pit wall. Following are the factors which are considered to determine the value of break-even stripping ratio (BESR) = (A-B) / C
A - Revenue per tonne or ore
B - Production cost per tonne of ore (including all costs to the point of sale, excluding stripping)
C - Stripping cost per tonne of waste
In certain cases, a minimum profit is requirement is included in the formula and break-even stripping ratio is calculated as
BESR = [A - (B+D)]/C
Where C is minimum profit per tonne of ore.
Break-even stripping ratio is an important measure for mine to operate economically profitable. A mine's operation is measured economically by NPV (Net Profitable Value). As the mine life progresses, the minable ore gets deeper and stripping ratio reduces as the overburden increases compared to minable ore. From economic front, the cost of transportation also increases as the pit deepens because more fuel / energy is required to carry out or remove the overburden from mining site. The pit limit is decided or estimated initially to determine the maximum depth until which the mine is economically profitable. The production cost of ore depends on the cut-off grade of the ore. If the cut-off grade of ore reduces, the effective metal or mineral outcome per tonne of ore processed also reduces, hence the cost of production for equal amount of metal outcome decreases. Mine planners considers many factors while determining the economics of mine for a profitable production, these parameters are:
I. Stripping ratio (ratio of waste or overburden to ore)
II. Depth of mine or overburden for removal
III. Thickness and variability of ore seam
IV. Total quantity of reserves
V. Cut-off ratio of ore i.e. % useful metal per tonne of ore
VI. Ore grade
VII. Moisture content inside the ore
VIII. Selling price of mineral or metal (dynamic)
IX. Transportation cost of overburden
X. Capital cost investment needed
XI. Production rate
XII. Random unforeseen failures
WORK TOGETHER WITH EXPERTSMIND'S TUTOR TO ACHIEVE SUCCESS IN ENGIN2503 MINING ENGINEERING ASSIGNMENT!
7. What is difference in opencast, open pit and quarry mining?
Open-pit mining is a technique of surface mining in which an excavation is made on the surface of earth to extract commercially viable ore. This excavation is called a pit and it is open on the ground hence called an open-pit. In Open pit mining, the overburden (OB) transported to waste dump & use same equipment for stripping OB & mining mineral/ore.
Open-cast mining is another type of mechanical extraction process under surface mining methods in which an excavation is made which goes at much higher depths compared to open-pit mining method.
The first and foremost different between open-pit and open-cast mining method is, open pit is used for shallow depths while open-cast is used for higher depths. Second important difference is, in open-pit mining, the waste or overburden is transported out of the mine while in open-cast mining, overburden is not transported to waste dump but cast directly into adjacent mind panels. In Open pit mining, the overburden (OB) transported to waste dump & use same equipment for stripping overburden& mining mineral/ore. In open-cast mining method, separate equipment for stripping overburden& Mining mineral/ore.
Quarry mining is a type of open-pit mining which is used for extraction of building materials such as limestone and dimension stone. Quarries are usually made at much shallow depths compared to open-pit mining. There are many different types of building materials extracted for which quarries are planned some of which are Granite, gypsum, Quartz, sandstone, Chalk, Sand, gravel etc.
A tabular comparison of open-cast mining, open pit mining and quarry mining are as follows:
Open pit mining
|
Quarry
|
Underground mining with shaft
|
Done for those minerals which lie close to the surface of the earth
|
Used for mining minerals at shallow depths
|
Minerals which lie at great depths below the surface of the earth
|
Used where commercially useful minerals are found near the surface.
|
Used for extracting building materials like stone and limestone.
|
Used where the minerals occurs as veins in hard rock deep below the surface of the earth
|
Extracted using Earth moving machinery
|
Extracted using Earth moving machinery
|
Extracted using elevators which can carry people and mineral extracting equipment deep into areas where minerals are available
|
Overburden is removed and taken to waste-bin after the removal
|
Overburden is comparatively very small and carried out of the pit
|
The overburden is not taken out instead it is casted back in the original place after mining
|
8. Briefly describe frontal cut, drive-by and stop-and-reverse parallel operations.
In open-pit mining, frontal cuts are used to increase the lateral depths of the mines. Lateral extension are most conveniently done by frontal cuts. In frontal cuts, adjacent niches of the mine walls are cut into outcome pile instead of huge excavators moving along with mining outcomes. Frontal cut is illustrated and explained in the figure below:
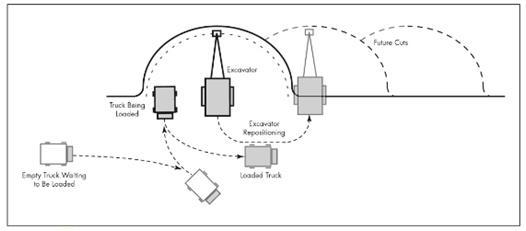
Schematic of frontal cuts
Parallel cuts are the most common ones in which an excavator moves parallel to the bench walls cutting into the walls of bench and creating musk pile which is removed parallel to cutting. In drive-by operations, the trucks are moved in a straight line and without moving inside the line of excavator. The disadvantage of drive-by operation is, it required comparatively larger amount of space over the bench for operation. It is shown in figure below.
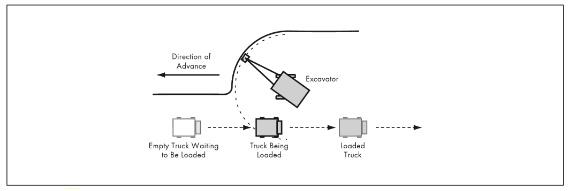
Schematic of Drive-by operations
In stop-and-reverse operations, space requirement is comparatively low. It is shown in figure below. In this type of operations. The trucks have to stop perpendicular to bench wall and reverse till the location of musk hill and get it loaded. This sequence is followed by each subsequent truck waiting to be loaded.
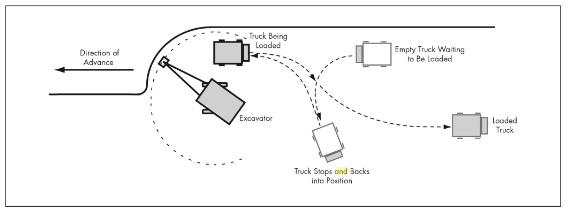
Schematic of Stop-and-reverse parallel operations
The overall operation of the mine is to be looked at to determine the type of transportation method needed to be selected. The haul road is to be designed as per the operation method selected. As stated earlier, Parallel cuts are the most space consuming removal method hence the width of haul road has to be sufficient to accommodate a continuous line of incoming trucks.
DO YOU WANT TO EXCEL IN ENGIN2503 MINING ENGINEERING ASSIGNMENT? HIRE TRUSTED TUTORS FROM EXPERTSMINDS AND ACHIEVE SUCCESS!
9. Explain the following terms with the aid of sketches, as they apply to an open-pit operation;
a. Overall slope angle
b. Bench stack slope angle
Overall slope angle - Overall slope angle is calculate using toe of bottom-most bench and crest of top-most bench. The line connecting above mentioned 2 points with ground is called overall slope angle.
Individual bench slope angle is the angle made line connecting toe of bench and crest of bench with ground. An open pit consists of several pits as per its design and over the life of the mine, more pits are being dig inside the mine.
Both the angle are shown in the sketch below for an open-pit mine. It shows the individual bench angle over a cross-section of mine.
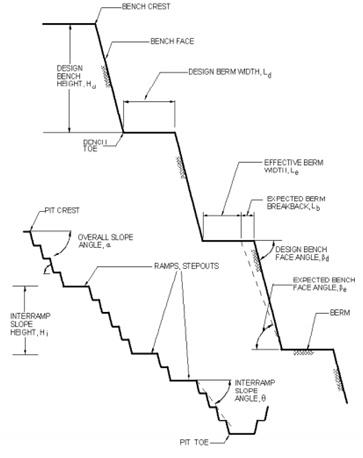
There are analytical equations available for calculations and relating bench angle, bench stack slope angle and overall bench angle. The overall slope angle is governed by the ultimate pit limit of open-pit design. There are different benching approaches available such as single benching, double benching or triple benching. When mine depth is shallow, the inter-ramp slope angle are very steep such that it may results in flattened slope of the pit, double benching can be used. Depending on the type of benching method used, the overall slope angle accordingly changes.
10. Why is the individual bench slope angle steeper than the stack slope angle, which is steeper than the overall pit slope angle?
Individual bench slope angle and overall pit slope angle are explained in previous question.
Stack slope angle is calculated between 2 consecutive ramps. A line connecting toe of bottom most bench and crest of top-most bench before the end of ramp, is drawn, the angle made by this line with horizontal is called stack slope angle. It is also called inter-ramp slope angle as shown in the figure below.
Individual bench slope angle is steeper than stack slope angle so as to assemble multiple benches in a tilted shape so that they are easily accessible one-after the other from the ramp.
The bench angle is steeper than overall slope angle. This is to give pit its tilted slope and shape of the pit. Bench angle of a pit depends on many other factors which are excavation output dependent.
When mine design is prepared, each of the parameter namely individual bench angle, overall slope angle and stack slope angle are to be taken into account. The overall mining plan is prepared with the help of automated computerized algorithms which sequence the mine cutting to reach the highest metal or mineral rich ore to be mined first and proceed accordingly [4]. The Bench angle is the angle made by the line connecting any bench's toe to bench's crest with the horizontal. When the mine planning is done, the bench angle is kept steeper so that all the bench are accessible from the hauling surface.
ORDER NEW COPY OF ENGIN2503 MINING ENGINEERING ASSIGNMENT & GET HIGH QUALITY SOLUTIONS FROM SUBJECT'S TUTORS!
11. A dragline is to be selected to remove overburden at a rate of 395,000 cubic meters per month. If it will be scheduled to operate 720 hours per month with an operating efficiency of 0.80, its bucket factor is 0.85 and its cycle time is 54 seconds, what should be the size of its bucket?
Draglines are used in surface mining which are mostly built on-site for strip mining operations to remove overburden and ore. It consists of large bucket which is suspended from a boom with wire ropes. The bucket is maneuvered by means of ropes and chains. The hoist rope is powered by electric motors and drag rope is used to draw bucket assembly horizontally.
Dragline overburden removal rate (P) = 395000 m3/month
Per month operating hours (U) = 720 hours/month
Operating efficiency = 0.8
Bucket factor (also called as fill factor) = 0.85
Cycle time (C) = 54 seconds
For total 720 operational hours in a month with 0.8 efficiency, hence effective operational hours for overburden removal = 720 x 0.8 = 576 hours
For required dragline overburden of 395000 m3/ month,
Per hour removal rate = 395000 / 576 = 685.764 m3/hour
If time required per cycle is 54 seconds, total number of cycles per hours = 3600/54 = 66.7 cycles/hour
Hence we can calculate the amount of overburden to be removed per cycle,
Amount of overburden per cycle = 685.764/66.7 = 10.29 m3
Since bucket factor (fill factor) is 0.85, hence actual bucket capacity for overburden removal
= 10.29/0.85 = 12.1 m3
The calculated size of the bucket should be 12.1 m3.
12. Describe briefly how the operational life of a mine can influence the choice of transport equipment. Refer in your answer to a new open-pit mine and a deep open-pit mine that is near the end of its production lifetime.
There are many types of transportation systems which are used in open-pit mining, some of which are
a. Ramp haulage (using cranes or trucks)
b. Shaft hoisting
c. Conveyors (vertical and longitudinal)
Ramp haulage is used in open-pit mines using mostly trucks to remove the overburden from mine pits. Ramps are made inside the mine which are accessibility roads which are made at inclined angles which are needed to carry traffic from both ways. For underground mining, shafts are used as a means of access and transport. Shaft hoisting uses a deep drilling mechanism which are used in underground mining that are to be run at higher production rates. There are different types of hoist that are used some of which are Drum hoist, Friction hoist, and blair multi-rope hoist.
The selection of optimum transportation system is necessary for profitable operation of the mine. Some of the most important factors which govern the transportation method in surface mining are:
- Reserved of ores
- Throughput of mine
- Type of mining method
- Ground conditions
- Pit design
- Price of selected transportation system
- Machine amortization rate
As the operational life of mine passes, the production rate as well as mine depth changes. In most of the cases, the production rate decreases and mine depth increases. For example, for a new open-pit mine, initially the production rates are high and mine depth is shallow. As the mining progresses, when the open-pit gets to end of its mining life, the production rate decreases and mine depth increases significantly. For a new mine, with low production rate, ramp haulage is termed as best transportation mechanism. Transportation system selection based on production rate and mine depth are shown below:
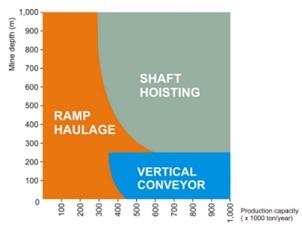
As the mine gets old and depth increases, depending on the production capacity, the transportation system can be shaft hoisting if the production is high.
GET BENEFITTED WITH QUALITY ENGIN2503 MINING ENGINEERING ASSIGNMENT HELP SERVICE OF EXPERTSMINDS.COM
13. Briefly describe the applications of the below equipment in surface mining. What are the major factors affecting the selection?
a. Mining shovel
A mining shovel is an earth moving equipment which is used in mining for digging and loading the mining outcomes. It is usually electrically powered in which a digging head in the front moves over the rock and breaks a large chunk out of it. There are hydraulic versions also which are used for higher loads requirements. These are usually mounted on revolving decks so that they can access complete circle in their vicinity.
Major factors affecting the shovel selection are, type of tasks (digging, lifting, dumping etc), type of ore, depth of mine and availability of power resources inside the mine [5].
b. Dragline
Draglines are enormous earth moving machines which are used by miners to remove the ore and overburden from mining sites. These machines can range from few hundred tonnes to thousand tonnes per pass. These are broadly of 2 different categories - draglines which are made out of lifting cranes that are assembled on-site and other ones are based on crawling cranes inside the open-pits.
Dragline consists of a bucket attached to a boom with metallic wires or ropes. The size of the bucket is the major factor deciding the dragline. It is calculated using site throughput, load factor, fill factor, stripping ratio and type of ore.
c. Bucket wheel excavator
Bucket wheel excavator is used in surface mining for continuous mining process. It is usually used for large-scale pit excavation. It consists of a large toothed wheel in front which which has scoops kind of shape on it. Once it starts mining, it scoops normal to wall boundary and takes out large amount of mine ore and does it continuously.
The bucket wheel is most important and load bearing component of the machine hence machine is named after this wheel mounted in fornt. It has a certain configuration of scoops which are sharp in the front. While rotating, scoops cuts the material and picks it up inside the scoop and then material is transferred along the boom of the machine.
Major factors that affect the selection of bucket wheel excavator are rock hardness, type of resource, production rate, design and pit scape available in mine, and depth of cut.
d. In-pit crusher
In-pit crusher is a machinery system which crushes and reduces the size of mined rocks to a size so that it can be conveyed out of the mine. Some of the in-pit crushers are accompanied by conveyor systems hence called in-pit crushers and conveyor systems. These could be semi-mobile, fully-mobile or completely fixed inside the pit depending on the application. They make removing the mined ore and waster easy to convey by reducing its size below a critical size.
This significantly reduced the movement of hauling trucks inside the pit since it continuously crushes and conveys out most of the mine output (ore or waste) for subsequent processing.
The factor needed for deciding the in-pit crusher are required throughput (tonnes/hour), Truck quantity, Type of crushers, minimum size of rock crushed, and unit crushing cost.
e. Rail haulage
Rail haulage is a convenient transportation system used in under-ground mining to remove the mining outcome (ore, coal or waste) to the nearest processing plant. These are not feasible at many mining location due to their geographical limitations. If the processing plants could not be set-up near to the mine, rail haulage becomes the most suitable option to carry-out mining outcomes.
Major factors deciding selection of Rail haulage as a transportation system is, Mine throughput, geographical feasibility, distance of plants from mining site, operational life of the mine.
f. Truck
Trucks are used in mining industry for mined ore and overburden removal from mining site. Usually in open-pit mining, trucks are used and a special haul road is designed for movement of trucks inside and outside of the mining pit.
Major factors deciding selection of truck are, carrying capability, durability and reliability, ease of operation, mileage and availability.
g. Conveyor belt
Conveyor belts are automated moving lines which can carry crushed outcomes from mining from mined site to nearest plant or dumping site. The first use ever of a conveyor belt was done inside a coal mine to carry out the outcomes. Conveyor belts are most convenient and reliable way of transporting the mining outcomes back to plant to dumping site.
Major factors deciding the selection are type of mining output, mining throughput, type of geographical location and distance of plant from mining site.
14. Explain the importance of slope angle in economics of surface mines by some example.
Slope angle are one the most critical parameters which is needed for fail-safe working of open-pit mine. There are 3 main approaches or methods which are considered to design - Factor of safety, probability of failure and risk analysis.
If open-pit mine fails for halts for some time due to design faults, it economics suffers severely. As per classical definition - 'Quantification of the economic impacts of slope failure with reference to the loss of annual profit or total project value as measured by the NPV'
There are quantification approach available to calculate the impact on total profit, in case of a slope failure. NPV for a mine is the total discounted annual profit for entire life of a mine which is estimated based on initial design of a mine and also scheduling and operations planning of the mine.
If a slope fails during working of a mine, its economic impact is in terms of disruption or halting of production / excavation from mine. The ore extraction from the mine stops for certain amount of time until the slope or bench can be fixed again and excavation work starts. If a slope angle fails during mine's working time, the economic impact can be calculated using following equation:
Failure impact = NPVreference - NPVwith slope failure
Where NPVreference is NPV of mine planned without failure, and NPVwith_slope_failureis after the slope failure has occurred.
In short, slope failure impacts:
- Disruption of ore extraction and feed to plant leading to idle time
- Additional cost to repair site and restore working
Figure below shows an example of conceptual basis how the slope failure can impact the economics of mining.
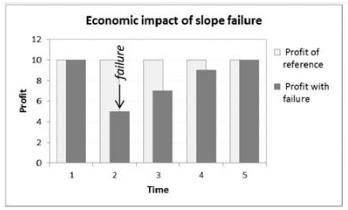
Depending on the time during the entire life of the mine where the failure occurs, the impact of economics accordingly changes. Figure below shows the effect depending on the year in which failure happens.
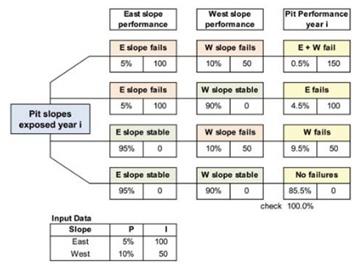
ORDER NEW ENGIN2503 MINING ENGINEERING ASSIGNMENT AT NOMINAL PRICE!
15. A discontinuity is found fully developed from the toe to the bench surface on a 20 m high slope, slope angle 63°. The discontinuity (frictional angle 32° and cohesion 20 kN/m2) is planar and its strike is parallel to the slope face with a dip 42°. Determine the factor of safety in case of a planar slope failure assuming drained conditions. Unit weight of the rock is 2.7 t/m3
Discontinuity developed from toe to surface of the bench
Bench height (H) = 20 m
Bench slope angle (ψf) = 63°
For discontinuity, Friction angle (φ) = 32°
Cohesion strength (c) = 32 kN/m2
Discontinuity strike is parallel to slope face with a dip of 42°
Angle of failure surface from horizontal (ψP) = 42°
Unit weight of rock (γr) = 2.7 tonne / m3
Overall schematic of discontinuity is shown in figure below, except the difference is that current case is in drained condition.
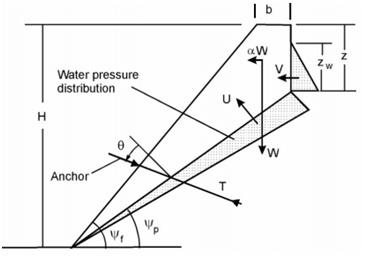
If W is the weight of rock resting on resting on failure surface, then W is
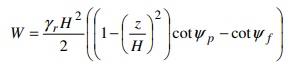
Where
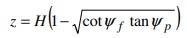
Calculated value of z = 4.955 m
W = (2.7/2) x (20)2 ((1-(1/20)2)cot(42) - cot(63))
= 287.8 tonne/m2
Value of A,

A = 22.485
Horizontal earthquake acceleration, α = 0.08g = 0.08x9.81 = 0.785 m/sec2
Factor of safety is given by:

F = 11.312
NEVER LOSE YOUR CHANCE TO EXCEL IN ENGIN2503 MINING ENGINEERING ASSIGNMENT - HIRE BEST QUALITY TUTOR FOR ASSIGNMENT HELP!
16. Illustrate bench width. Why should we provide safety bench? What are the factors affecting the width of safety bench?
The Bench Width governs the wedge size in a mining pit. It is measured as the horizontal distance fromtoe of the slope to crest of the previous bench.
Bench width is a limiting value in a pit design. Bench width should calculate a smaller wedge compared to what is calculated by slope height or other pit parameters.
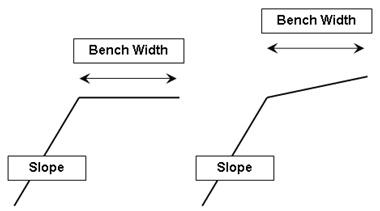
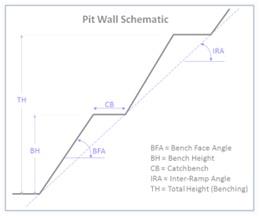
As shown in the schematic above, bench width is the horizontal width provided at the bed of a bench for mining access.
Safety bench or Catch bench is provided in pit-mine to catch a rolling or spalling rock and stop it to the bottom of the pit. There are rule of thumbs to calculate catch bench width which is 4.5m + 0.2H, where H signifies height of the bench. Using this, we cancalculate catch bench width for a bench height of 5m is calculated to be 5.5 m. This is only rule of thumb which can be modified based on many other factors which may govern width of safety bench.
17. What is pit limit? Describe a procedure to determine pit limits.
Pit limit is the maximum vertical or longitudinal length until which the mining of an ore deposit by surface mining, can be carried out with economic viability.
The pit limit is decided by cost of removing overburden from the pit compared to cost of total mined ore. If the over-burden removal cost exceeds the cost of ore removed from mining, then it is called pit-limit.
Pit-limit are usually decided with the help of automated of automated computer codes. Manual procedure is described here. Pit limits are governed by break-even stripping ratio. At the point where, cost of overburden removal becomes equals to cost of ore removal. Once the mining is started or planned, at any point, instantaneous stripping ratio is calculated and pit depth is increased until instantaneous stripping ratios becomes equal to break-even stripping ratio.
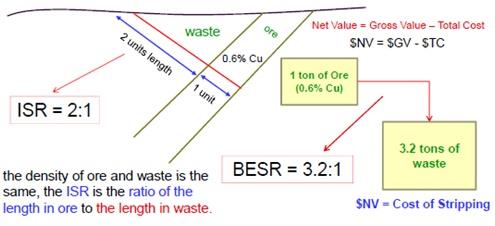
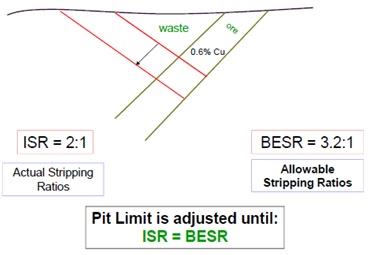
The other determining factor which also plays a critical role in deciding pit limit is the price of ore or metal in question. The metal price keep fluctuating as the mine life progresses and it might be possible that initial designed pit limit becomes economically infeasible considering the Net Profit Value as the metal price decreases. In global market, the price of the metal is determined by the demand vs. supply trends. In mining operation and planning, it is necessary that a fixed amount of duration is decided for the Net Profit Value to be assessed. This reevaluation may increase or decrease the ultimate pit limit of the mine depending on the current metal price. Many decision making approaches are available for mining engineers to determine the economically feasible pit limit. For a given natural resource needed, many literature suggest different decision making approaches to be used for in the case of uncertainty. Real Option Approach (ROA) is one approach for decision making on actual pit limit for an open-pit mine. The break-even stripping ratio usually gives a clear direction given many variables affecting overall profitability of the mine. For mine planners, it is now become of utmost importance to keep updating the production schedule as per latest NPV of mine and current Break-even stripping ratio depending on the global market conditions. Many commercial software are available now to make it a streamlined process to design a pit and determine ultimate pit limit. Lerchs and Grossmann came out with an optimization algorithm which can be programmed for a number of inputs to mine planner to keep the mine operations profitable by maintaining significant cash flow. Lerchs and Grossmann used a parameter in NPV to optimize cash flow. This parameter is the amount which should be reduced by each block's economic value. When this parameter becomes zero, the correct pit limit is determined for the open-pit.
18. Estimate the unit profit in mining and processing a 0.80% copper ore deposit if the selling price of copper in concentrate is $1.73/kg and overall unit costs are $6.5/ton. Overall recovery is 82%. Calculate the cut-off grade of the copper deposit.
Metal sale price (s) = $1.73 / kg
Metal recovery (y) = 82% = 0.82
Cost to process ore (C) = $6.5/tonne
1 Unit = 1 tonne = 1000 kgs.
With 0.8% copper, in 1 tonne of ore, amount of copper = 1000 x 0.008 = 8 kg.
Selling price of per unit ore (8 kg copper) = 8 x 1.73 = $13.84
Processing cost per unit ore = $6.5
Profit per unit of ore = $13.84 - $6.5 = $7.34
Cut-off grade = C/(y(s-r) = 6.5/0.82(7.34x1000) = 0.001 = 0.1% copper ore deposit
ORDER NEW ENGIN2503 MINING ENGINEERING ASSIGNMENT & GET 100% ORIGINAL SOLUTION AND QUALITY WRITTEN CONTENTS IN WELL FORMATS AND PROPER REFERENCING.
19. A surface mine operators needs to purchase a front-end loader that will be used to load ripped coal onto on-highway dump trucks. The mine operates two 7 hour shifts per day, 5 days per week, and 50 weeks per year. The daily production of coal is 1500 tons. The desired cycle time is 1.0 min or less. The density of loose coal is approximately 1.0 t/m3. Assume that the load factor is 0.65, the bucket factor is 1.23 and the operating factor is 0.75. What bucket size is required?
Per year working hours = 50 x 5 x 14 = 3500 hours/year
Desired cycle time = 60 seconds
Number of cycles per hour = 3600/60 = 60 cycles/hour
Density of coal = 1 tonne/m3
Load factor = 0.65
Bucket or fill factor = 1.23
Operating factor = 0.75
Effective working hours per day = 14*0.75 = 10.5 hours/day
Coal production = 1500 tonnes/day = 1500/10.5 = 142.86 tonnes/hour
Since there are 60 cycles per hour, hence
Coal production per cycle = 142.86/60 = 2.381 tonnes per cycle
Volume of bucket or bucket size = 2.381 / 0.75 x 1.23 = 3.9 tonnes
20. Assume an underground mining cost of $25.5/ton ore for an orebody. Assume open pit mining costs at $0.0028/kg ore removal and $0.0035/kg waste removal. Determine the stripping ratio for an open operation that results in break-even cost differential between the two mining methods
For underground mining, Mining cost = $25.5 /tonne ore
For open-pit mining,
Ore removal cost = $0.0028 /kg.
Waste removal cost = 0.0035 /kg.
Open-pit Stripping ratio = 0.0035 / 0.0028 = 35/28 = 5/4 = 1.25:1
For underground mining,
Ore removal cost = $25.5/1000 per kg = $0.0255 / kg
For break-even, ore removal cost = overburden removal cost
Hence stripping ratio for break-even between the 2 methods = 0.0255/0.0028 = 9.1:1
GET GUARANTEED SATISFACTION OR MONEY BACK UNDER ENGIN2503 MINING ENGINEERING ASSIGNMENT HELP SERVICES OF EXPERTSMINDS.COM - ORDER TODAY NEW COPY OF THIS ASSIGNMENT!
21. What is the purpose of pit limit optimisation and typical computerised optimisation methods?
Pit limit optimization is a technique to optimize the maximum pit limit to make the mining commercially beneficial with highest NPV. There are multiple definition of maximum pit design depth or pit limit, most acceptable of which is, pit limit optimization is a balancing act between stripping ratio and the cumulative value in the final pit limits.Once the cut-off grade for the open-pit mining is fixed, there are various methods such as Lerchs-Grossman and others and others which can be used to calculate the economically feasible ore-blocks that can be excavated using open-pit mining methods.
The typical open-pit design process is shown in figure below:
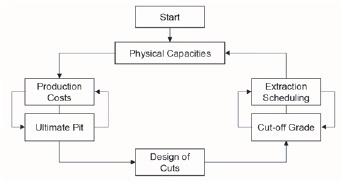
There are 2 most famous computerized methods for open-pit limit optimization:
(1) Floating cone method (Laurich, 1990)
(2) Maximum weight closure algorithm defined by Lerchs and Grossmann (1965)
Method 1 which is floating cone is less used and Method 2 is widely famous and used by many computer programs. Method 2 uses a network structure to produce an optimal solution of pit limit determination. In method 2, starting inputs of an initial ore deposit which is modeled as a block inside the algorithm, the Lerchs and Grossmann algorithm calculates the optimal pit shape and pit limit by identifying the overlying blocks which must be removed sequentially to each block inside the entire block or site. A typical example of computerized open-pit limit optimization is shown in figure below:
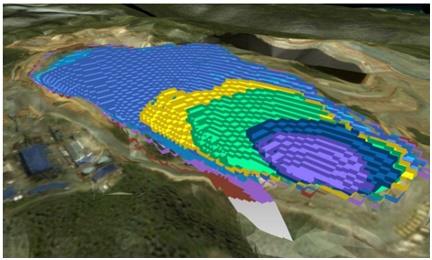
22. What are typical mine wastes? Describe measures to safely contain mine wastes.
Mining generates huge amount of waste some of which can be substantially harmful to environment while some waste might not. Some of the mining wastes are even used for other purposes such as building materials and refill. The typical composition or type of residue mineral contained inside the waste decided the type of waste and its management method. If not managed properly, these minerals can react with adjacency and can be very harmful for overall environment and local communities.
Waste happens in multiple stages during mining process and during overall life of mine, from the first exploration of the mine until the last processed material before mine closure. Many mining wastes are generated out of which three significant onces which are generated in large amount are, (1) waste rock, (2) tailings and (3) mine water. Along with these wastes, there are many chemicals used inside the mine such as cyanides and explosives which are additional mine wastes. They also account of small fraction of the total mine waste, but are much more severe risk due to their high toxicity. The main mine waste types and measures to safely contain them are described below:
A. Waste rock -Waste rock is the rock that is excavated to reach the ore. It depends on the geometry and location of the ore body in the mine. Since these are bulky waste and usually are produced in the stripping ratio of 2:1, they are stored pretty near to the mine. Waste rock may contain elements like mercury, compounds of nitrogen and ammonia, and some other components few of which could be very toxic.
B. Tailings -As the ore gets processed and the valuable minerals gets separated, a fine-grained mineral sand remains as waste, called tailings.It is usually taken out from the mine in the form of slurry. The amount of tailings generated depends on the grade of ore. If the grade of ore is 2, means there would be 98% tailing in the ore and 2% mineral or metal.
Tailings are usually stored in specifically made tailing storage facilities (TSF). There are different types of TSFs made depending on the composition of tailings. The boundary of TSF are usually made with the waste rocks from mine. The waste rock needs to be non-acid generating rock (NAG) to ensure long-term stability. Sometimes the embankments include a layer of geo-membrane, a type of synthetic liner or barrier with low permeability, which is mainly used to stop the fine-grained tailings from seeping in to the coarse waste rock.
C. Mine water -Water is an essential resource used in mining work. Few of the mining operations such as drilling needs significant amount of water. During mining, water gets contaminated with harmful minerals and metals.
Water should be recycled as this is important resource. Water treatment facilities are established nearby the mines.
There are many global norms which change from land to land on managing mine wastes. Mineral waste management has become a popular topic of research with more stringent norms coming in for waste management. The old practices of waste management has around linear economy but now since it has changed to more of circular economy, the practices has to be modified accordingly. The mining waste management system relies on type of treatment and kind of waste produced by the mine. With mining planners now taking waste management costs into account, the overall operational cost of the mines are more corrected. Many of the countries which are resource rich, does not have local stringent norms for waste management hence a global policy for waste management becomes necessary. There has been tremendous improvement in mining waste management since its inception in 1980's where initially all the mining waste used to simply dumped into cleaner natural resources or land fillings.
Rehabilitation of mining location after shutting of mining is also an important norm. This depends on the type of ore being extracted from the mine. If the ore contains toxic element such as nitrides, sulfides, it has to be properly covered with thick layers of non-toxic wastes such as clay, rocks etc. so that during rains, it does not react with fresh water and reach sources of drinking water. There are many acid drainage which are made out of water resource being used at the time of mining. During mining, these are stored locally but as the mine life nears its end, It has to be covered in such a way that it does not harm local communities around it. The open-pit are also fenced after required filling so as to avoid any harm or mishap with open-pits. It is also made sure that the levels of any toxic waste does not reach ground water levels.
DO WANT TO HIRE TUTOR FOR ORIGINAL ENGIN2503 MINING ENGINEERING ASSIGNMENT SOLUTION? AVAIL QUALITY ENGIN2503 MINING ENGINEERING ASSIGNMENT WRITING SERVICE AT BEST RATES!
23. Briefly describe:
a. Objectives of production planning
Production planning is among the most important tasks in mining to optimize the Net present value (NPV) with the available resource constraints. There are 3 main objectives of production planning -
(i) Mine-block sequencing
(ii) Ore-waste or Overburden segregation based on cut-off grades for ore
(iii) Determining optimum production rates
There are many methods or algorithms available which based on available inputs prepares a production plan over entire mine life. Mine block sequencing is a complex problem because of number of parameters affecting it and many variables such as metal price disturbs the optimum sequence. To meet economic goals for continuous profitable run of a mine, it is necessary to address all such uncertainties at regular intervals. Production planning, if done properly, can help maintaining a healthy NPV of a mine keeping the investment goals intact. For a mine planner, Production planning is a complex multi-objective optimization problem. Overall a mine is seen as a combination of ore blocks which are to be sequenced in such a way that with minimum time and overburden, the output metal should be maximum, i.e. stripping ratio should be highest. To address this, many optimization algorithms have been developed and computerized with the advent of digitalization. Multi-objective iterative greedy algorithm is found as the most recent advancement in the field of production planning. Decision making for optimum mine-block sequence is a very complex problem to be handled manually. Older procedure was to use rule-of-thumb for such optimization but many a times, this does not account for realistic scenario which are all dynamic. It has been proven numerous times that with automated algorithms, the overall NPV of a mine can be improved by upto 10% compared to manual procedures. Among many, there are a few most critical parameters that should be addressed at prime importance, which are:
I. Geological ore samples - Cut-off ratio for the ore
II. Overall infrastructure available for production i.e. production capacity
III. Available manpower
IV. The global demand and price of current ore or metal in question (including fluctuations based on past data)
V. Overall production overheads
VI. Local land norms of waste management
VII. Transportation needs depending on the type of mining method selected
b. Taylor's mine life rule
Taylor, a mining engineer by profession, gave a mine life determination rule based on an empirical formula. There were many theories earlier which were based on economic theory and determining Net Present Value (NPV) to decide the optimal mining rates but unfortunately, they were not applicable in reality as they gave unrealistic results. Taylor, with experience of over 30 projects, developed an empirical relationship applicable to a vast range of mine types. Since it was derived from experience, it was more applicable and realistic compared to theoretical methods.
The empirical formula derived by Taylor for mine life estimation is given by:
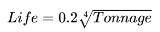
Equation of production rate is given by:

Taylor assumed that a mine working 350 days in a year, then according to taylor's law:

Before taylor's equation, the mine life determination based on theoretical methods had rendered many production mine to go economically unviable after few blocks of mining. The capital cost required for mining deeper ore blocks, increases rapidly with depth. Hence to maintain a profitable production rate had become a difficult problem for mine planners.
Although, taylor's equation is based on reality, there are many studies which have rendered this formula unacceptable. There are a few limitation that this equation carries, which are:
I. Applicable till a certain depth of mine, can not be really applied for very deep mine where production is limited by hoisting limits of shafts
II. Production rate is completely made dependent on discovery of blocks hence results of erratic results of production rate and mine life determination
III. It limits the production rate by the depth of the mine
IV. It cant be applied for very large production rate (<200 metric tonnes) as this rule rate them as unfeasible.
c. Sequencing by nested pits
A nested pit analysis is performed to obtain discounted optimal pit limit i.e. optimal NPV. This is a technique used in computerized optimization algorithm of pit limit. Basic idea behind this analysis is to get nested pit shells and a sequence to mine them so as to get the highest Net Present Value (NPV) from the mine. It is done by incrementing the commodity price throughout a range of values around the base price. This takes many other inputs into account which are production planning, production scheduling, annual productivity targets, discounting, and recurring capital costs.
Traditionally when open-pit optimization is performed, it usually revolves around determination of ultimate pit limit. This results in manageable divided blocks of ore which should be mined in a specified sequence. If planned in an optimum way, they can increase the overall Net Present Value (NPV) significantly. This is done by economically applying an discount rate onto the planned blocks.
d. Production scheduling
Production scheduling is done along with production planning with the objective of optimizing Net Present Value (NPV). In production scheduling, different mining tasks are scheduled so to to optimize following objectives:
I. Block sequencing
II. Ore-waste discrimination
III. Optimization production rate
GETTING STUCK WITH SIMILAR ENGIN2503 MINING ENGINEERING ASSIGNMENT? ENROL WITH EXPERTSMINDS'S ENGIN2503 MINING ENGINEERING ASSIGNMENT HELP SERVICES AND GET DISTRESSED WITH YOUR ASSIGNMENT WORRIES!
Get best Federation University Assignment Help Service for related courses and units such as:
- ENGIN5504 Mine Environment Engineering Assignment Help
- ENGIN5514 Production Drilling And Blasting Assignment Help
- ENGIN5503 Advanced Mine Ventilation Assignment Help
- ENGIN5507 ORE Reserve Estimation Assignment Help
- ENGIN5506 Advanced Rock Mechanics Assignment Help
- ENGIN5502 Advanced Rock Breakage Assignment Help
- ENGIN5513 Materials Handling And Hoisting Assignment Help
- ENGIN5508 Smart Engineering Technologies Assignment Help
- ENGIN5515 Tunnelling And Mine Development Assignment Help
- ENGIN5501 Mine Safety & Environmental Engineering Assignment Help
- ENGIN5512 Underground Production Systems Assignment Help
- ENGIN5511 Mine Surveying Assignment Help
- ENGIN5510 Company Economics And Finance Assignment Help